Enterprise Minnesota President and CEO Bob Kill is an enthusiastic cheerleader for automation, but he has concerns about how some manufacturers have approached decisions about new technologies.
“We started to see our clients rushing toward automation during COVID because they either couldn’t have as many people on site as they wanted, or they couldn’t find people to work for them,” Kill says. “Sometimes I think it’s reverse decision making. We decide to invest in something, and then we rationalize what it’s going to do for us and why it’s going to be valuable.”
The urgency to reduce the burden on employees or to fill gaps left by a tight labor market led some manufacturers to purchase and install promising technology that didn’t always boost the company’s value or solve the problem at hand, and often left wasteful practices in place.
To prevent that type of cart-before-the-horse decision making, Enterprise Minnesota consultants began developing an employee-driven, step-by-step methodology to maximize the impact of automation. The result is VESSA, Enterprise Minnesota’s proprietary approach that involves five steps: assessing the source of value in the company; eliminating waste; standardizing; simplifying; and finally, automating. It’s aimed at laying a foundation for automation that helps manufacturers maximize the value of any new technology adopted.
“VESSA leads to more strategic and thoughtful use of automation,” Kill says. “Skipping the VESSA process can lead to automating inefficiencies and deficiencies inherent in the manufacturing flow.”
Employees at the center
While every step in the VESSA approach is important, involving manufacturing employees from the very beginning is the key to success, Kill says.
“You need employees involved at every step. When the people closest to the issue are driving the changes, you’ll have the best outcomes,” Kill says, adding that it boosts morale as well. “Engagement and satisfaction reach a whole new level when you trust and rely on your employees to make these changes.”
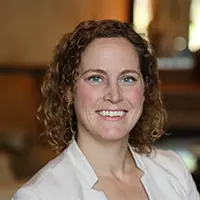
Ally Johnston, a business growth consultant at Enterprise Minnesota who helps companies evaluate automation options, adds, “You want the whole organization to understand the value stream and the strategic initiatives, because then we’re all pushing in the same direction.”
Johnston specifically encourages manufacturers to engage employees to identify waste and suggest opportunities for improvement. “They’re the ones spending minutes searching for a tool, continuing to get poor quality from a supplier, not having a maintenance plan so a machine is constantly down,” she says. “We need those subject matter experts to be suggesting improvements.”
Start with value
John Connelly, vice president of consulting at Enterprise Minnesota, says that embracing VESSA allows manufacturers to link value and continuous improvement with opportunities for automation. Identifying value — the “V” in VESSA — is a key first step, he says.
“Think about the services you perform or the products you produce most often,” he continues. “Pick one and then start applying continuous improvement — eliminate, simplify, and standardize. With the process tightened up like that, you are in a great position when you get to automating.”
Kill says the way the VESSA steps are woven together forces manufacturers at each step to think about the next letter, ensuring nothing falls through the cracks. Starting with identifying value makes sense, he says, because it typically leads to finding waste — those items or actions in the process that are wasteful or not adding value.
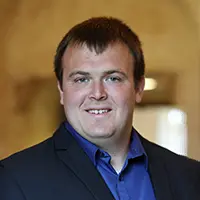
After eliminating waste, companies should consider ways to simplify processes. Eric Blaha, an Enterprise Minnesota business growth consultant, says simplifying really means error-proofing.
Blaha suggests a thorough review —again, driven by those employees closest to the process. It should include eliminating unnecessary steps, replacing tools or processes with more efficient approaches, preventing errors before they occur, facilitating improved processes with better guidance, detecting errors before they disrupt production, and mitigating the effects of challenges that cannot be prevented.
Next up is standardization, Johnston says. She points out that quality production is often kept on track through human intervention — extra steps that aren’t part of the process and can lead to inconsistency.
“When I hear words like Band-Aids, workarounds, adjustments, or tweaks, that says they’re doing these things that aren’t standard. They don’t flow and there’s a lot of variation. They have to intervene to make that good part,” Johnston says.
Before implementing automation, manufacturers need to eliminate those extra steps. With standardization, every process is repeatable, no matter which employee is completing the task.
Expand the definition of automation
With value determined and continuous improvement efforts in place, companies can evaluate where automation will yield the best returns. As automation became a buzzword in recent years, Kill says, some manufacturers only thought of robots or other fancy equipment. “Automation is so broad — it’s ERP systems, it’s putting tablets on the shop floor versus paper tracking, it’s digitizing records so they can be analyzed more easily,” he says.
Enterprise Minnesota defines automation as any change that reduces or eliminates human interaction. With that definition in mind, the VESSA philosophy supports a broad range of efforts, and the result is a thoughtful, strategic, systematic approach to making major investments.
The steps of VESSA could be useful on their own, even if an automation decision isn’t under review. But once a company begins considering automation, the cost — in equipment, training, and time — makes VESSA even more important. “If you don’t do it right, it becomes a much more costly error if you’re adding automation,” Kill says.
On the other hand, he says, “you may arrive at the end of VESSA and realize you don’t need to buy this technology, but you do need to do this other thing. That’s the value of the approach.”
VESSA in action
Kill describes a manufacturing operation that recently installed a new technology to solve a thorny production challenge. The process had required heavy lifting and complicated assembly that involved exact placement and many pieces, making it difficult to complete manually. “It had become a bottleneck in the overall process, was very loud and borderline dangerous, and a job that very few people wanted to do. Naturally, there was a lot of turnover in that position,” he says.
“They stepped back and thought about how that task fit into the process. They looked at the whole cycle, from beginning to end, and decided they could automate that aspect of it,” Kill says.
“It wasn’t about automating super-fast processing. It was about eliminating a difficult job that no one wanted to do, and the result is that now it’s no longer an issue. It’s no longer creating turnover. It’s no longer a situation that would be considered unsafe, and the process disruption is under control,” he says.
Kill points to ERP systems as another opportunity for VESSA to maximize outcomes. “A common thing you’ll hear from many manufacturers is, ‘We hate our ERP system,’” he says.
“Part of the reason is because they’ve skipped steps. They didn’t look at how their ERP system could increase value, and they didn’t go through the steps of eliminating waste, simplifying, and standardizing,” he says. “I bet if companies went through VESSA many would find they just aren’t using their current ERP system to its maximum potential.”
Return to the Winter 2024 issue of Enterprise Minnesota® magazine.