The suggestion box at Clearwater Composites, a Duluth-based company that manufactures customized carbon fiber components, isn’t a box at all. It’s a “continuous improvement board” on which the company’s not-quite 40 employees can suggest changes to different areas of the business. Anyone can see the suggestions as they walk past the board, and the business’ leaders review those suggestions every other week and implement them as they see fit. Ideas that don’t make the initial cut end up in a figurative “parking lot” on one side of the board for future consideration.
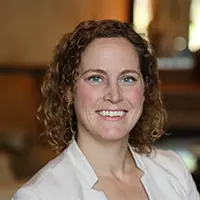
The principle is the same — a low-pressure way to propose improvements — but the implementation is different. Ally Johnston, a business growth consultant at Enterprise Minnesota who’s been working with Clearwater for about six months, says the board is actually the “opposite” of a suggestion box.
“The suggestion box is a black hole,” Johnston says. “People put things in and they’re locked. We want these to be visual. Anybody can read any idea. It’s meant to be engaging.”
The board is one of several concepts Johnston has pitched to Clearwater as part of a suite of “lean” manufacturing principles to get employees thinking about ways to thwart waste.
“Eliminating waste through people,” she says.
The board is a relatively small change that can nevertheless bring incremental improvements to Clearwater’s bottom line.
Consider the company’s production of carbon fiber pool cues. Staff felt that measuring both the thickness and the weight of each cue after it was molded was redundant. If a given cue’s weight wasn’t correct, then that meant the thickness wasn’t correct either, and vice versa, explains Jeff Engbrecht, Clearwater’s president and founder.
Staff said the measurements represented wasted data, Engbrecht says. “And they were right, so we stopped doing it. It was a good catch by the team.”
Eliminating the unnecessary measurement saved hours of redundant work over the course of a month.
“That adds up,” Engbrecht says.
Beyond leaning up its operation, the staff at Clearwater is settling into a new facility in Duluth.
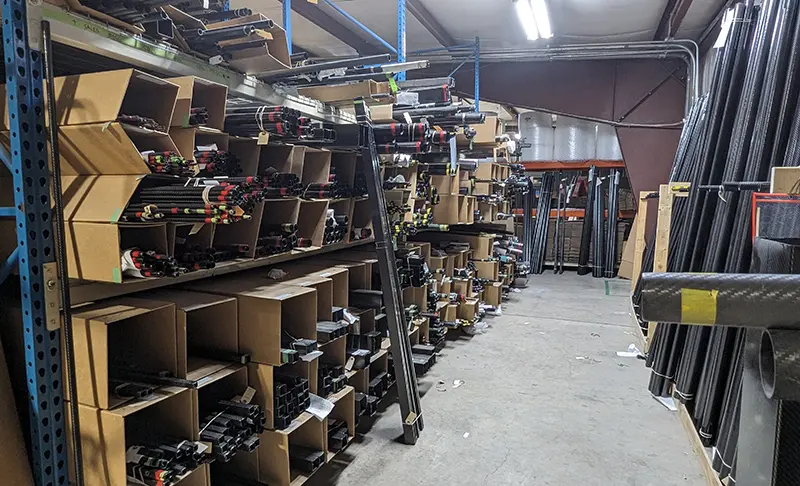
The company produces parts made of carbon fiber and other advanced composites for manufacturers across the United States. Those parts are used in precise measuring equipment, drones, sporting goods, custom bike parts, boats, guns, bows, and more.
Carbon fiber is lightweight but still strong and stiff, Engbrecht explains, and it can replace heavier materials such as steel or aluminum. It can also be designed to not grow or shrink as it gets hotter or colder, which makes it valuable for precision instruments that need an ultra-stable surface from which to measure.
Clearwater moved to the new facility in early 2022. It boasts about three times more square footage than the previous spot.
“We were space challenged,” Engbrecht says. “We had to make do with what we had.”
The new, larger facility means more storage space for raw materials, which helps insulate the company from supply chain vagaries, plus more space to cut larger batches of carbon fiber, as well as a planned second oven in which to cure finished carbon fiber parts.
The additional space also enables Clearwater employees to make and store new products, such as carbon fiber trusses. They can do more machining in-house as well, which means the company can produce carbon fiber tubes with slots or holes pre-machined into them at a customer’s request.
The company’s revenue has increased by about 50% since the move, Engbrecht says.
Johnston helped the Clearwater staff map out the company’s manufacturing processes and determine where else there might be waste.
They’ve also simplified training materials and work instructions for staff, particularly new hires. Clearwater’s documentation is thorough, of course, but could be overly technical or even overwhelming.
“Sometimes engineers don’t know how to explain things well to other people,” Engbrecht says with a laugh. “It was maybe a little too wordy. You’ve got to keep it simple and keep it in language that people can understand, but you’ve also got to make sure you hit the details of what’s important.”
The new process breaks down training materials into teachable, bite-sized portions that are easier to digest. That can mean training people better and more quickly. It’s part of the “job instruction” and “job method” principles of lean manufacturing, Johnston says — two more tools in the “house of lean.”
Clearwater and Johnston are currently contemplating a method to conduct “root cause analyses” to solve complex problems at their root, rather than finding Band-Aid-style workarounds. That can mean repeatedly asking “why?” to work backward, step by step, to determine the point from which a problem cascaded. The fifth “why?” usually reveals the root cause, Johnston says.
“Everyone in manufacturing wants to be a hero, they want to get the product out the door,” Johnston says. “They don’t necessarily fix the machine so it can’t break again, they’ll just put duct tape on it so it’ll still run.”
Return to the Spring 2024 issue of Enterprise Minnesota® magazine.