Spectro Alloys was at a crossroads about five years ago. The Rosemount company operated a thriving business recycling aluminum into casting alloys for foundries and die casters. But there was a looming challenge worrying company leaders. Electric vehicle design omitted the two largest aluminum castings — the engine and transmission. As the electric car industry revved up, Spectro’s automotive business could erode. Perhaps it was time to pivot.
Spectro began exploring new avenues for its business, led by company president Luke Palen and Tim Larson, the new executive chair of the board. The most promising candidates involved adding the technology and infrastructure to recycle post-consumer scrap aluminum like pop cans into higher purity aluminum of different shapes and sizes for sheet and extrusion products. They viewed it as a promising business that would help Spectro diversify its product lines and markets.
Their early research was prompted by concerns about how electric vehicles would affect Spectro’s market. “At the time, we thought our core business could be on a downhill trajectory, and we needed to counter that,” Palen says. “There was a lot of interest in aluminum sheet and billet for extrusion — that was clearly a growth trajectory. We started looking at this opportunity for expansion.”
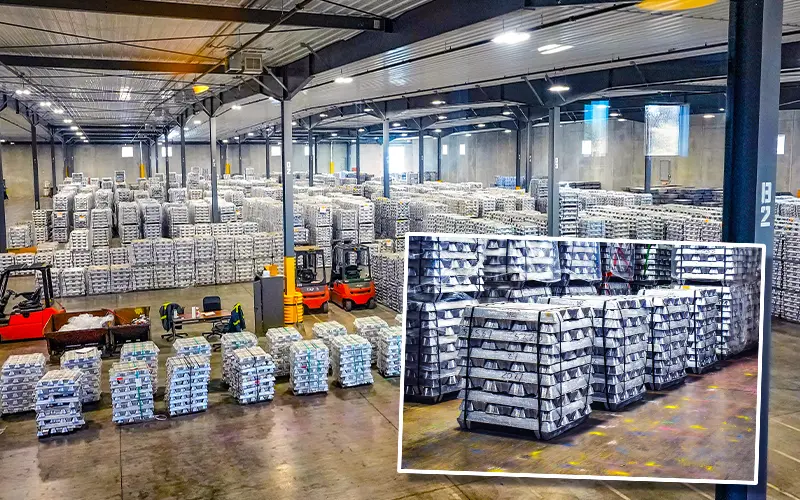
It turned out that their main fear was avoided. Innovations in casting and an emphasis on lighter vehicles led to new electric vehicle designs. They contain even more cast aluminum than internal-combustion vehicles while incorporating structural extrusions and sheet aluminum for the body. The headwinds facing Spectro also were diminished from surging interest in recycled aluminum and increased efforts by OEMs to reduce their carbon footprints. By the end of 2021, pandemic-related consumer trends helped make Spectro’s existing business healthier yet. Even with these positive indications, the company decided that augmenting its recycling capabilities was too good of an opportunity to pass up.
This year, Spectro will embark on a $71 million expansion that adds new processing and manufacturing capabilities. It’s working to have the 90,000-square-foot addition up and running in 2025, expanding its nearly 150-person workforce by 50 employees and adding 120 million pounds of additional recycling capacity per year.
The planned facility will give Spectro new customers and fresh products while bringing additional secondary aluminum supply chains closer to home. In addition, Spectro projects that its expansion could help improve aluminum recycling rates in Minnesota, where 45% of aluminum cans currently are recycled, Palen says.
The expansion builds on investments that Spectro made in the past decade, including in equipment to sort varied non-ferrous metals, says Greg Palen, a shareholder, board member, and Luke’s father. “We think it’s a good time to get into the business of making raw materials for sheet aluminum, which could be for the skin of a Tesla or a Ford F-150 or a beer can or soda can,” he adds. “We believe that electric vehicles will continue to gain traction. Now instead of one bucket of business we’ll have three buckets: casting alloys, sheet ingot, and billets for extrusion, like window frames, doors, or support parts for cars or ATVs.”
With this three-legged stool of recycled raw materials, Spectro will be primed to act on its mission to turn more secondary aluminum into new goods that people love and use every day. To do that, it will continue developing the recycling plant of the future to unlock environmental and economic benefits for Minnesota and beyond.
Making such a big investment can be a bit daunting, Greg Palen says, but he fully backs the plan and is excited about its positive prospects for Spectro. “It will make us a better, stronger company over the long term. With any new endeavor, and one that takes a lot of capital to put in place, there is some concern. I’ve got a lot of confidence in the team, and I think we’re doing the right thing to make the business thrive for the next 50 and 100 years.”
Always scrappy
Spectro Alloys specializes in transforming end-of-life scrap material mainly from cars and industrial uses into fresh secondary aluminum. An integral part of the recycling process involves separating aluminum from a variety of other materials, such as other non-ferrous metals, plastic, foam, and rubber.
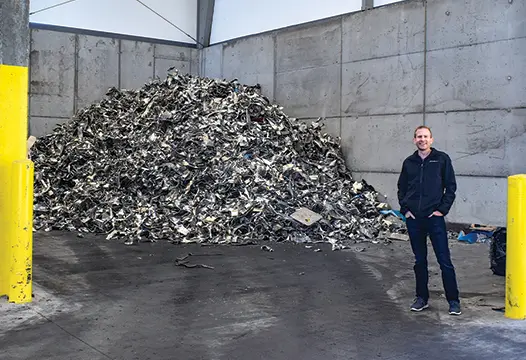
Think of an energy-efficient window frame. It’s often manufactured from extruded aluminum, with a thermal break made of plastic or rubber embedded in the metal. It requires specialized technology to process the frame by removing the non-metal elements, plus equipment to sort, clean, shred, and melt the aluminum, Luke Palen explains.
“If you bring your old, bent up ladder to a scrap yard, or your car gets sent to be recycled in Minnesota, it most likely comes through Spectro Alloys,” Palen says. “Then our customers will ultimately turn it into a new product that you could end up using every day. It could be part of your next car, appliance, lawn mower, light fixture, or ATV. Many of Minnesota’s most iconic brands rely on Spectro’s recycled aluminum alloys.”
Spectro Alloys has been at this work since 1973, beginning as a small scrap yard that melted aluminum for reuse. Greg Palen and his father already worked together on a heating and cooling company when Greg got the itch to try a new venture. He pulled together investments from his dad and others and bought Spectro in 1989. Palen viewed it as a promising and environmentally important business that had unrealized growth potential.
To unlock that potential, Spectro invested in technology to add more efficiency, automation, and pollution control that makes its work cleaner. A big part of Spectro’s investments involved focusing on improving the quality of its aluminum products and undertaking certification in standards like ISO 9001. This set Spectro up for success, says Vice President Gary Borner, a 34-year veteran who started out as a plant worker during college.
“It solidified that everybody knew what the processes were and that they were followed,” Borner says. “It was a good transition because not only was Spectro improving process-wise in the plant, we were gaining more visibility and more communication with a broader group of customers as a result of the certification process.”
In the 1990s and 2000s, Spectro grew its business with OEM and Tier 1 suppliers into the automotive and industrial sectors. Previously, the bulk of its customers were job shops and manufacturers with inconsistent needs for Spectro’s casting alloys. By focusing on Tier 1 suppliers, Spectro could ink annual contracts that provided more steady demand, along with a repeatable and reliable production schedule, Borner says.
In the 2000s, the trend of outsourcing manufacturing to low-cost countries had an impact on Minnesota die casters and foundries, with Spectro experiencing collateral damage, Luke Palen says. There were some tough years, including the 2008 Great Recession when some of Spectro’s competitors went through bankruptcy. Spectro stayed solvent and improved its sorting technology, pollution control, and other efficiencies, while focusing on expanding its domestic manufacturing clientele.
For example, investing in sorting technology enabled Spectro to expand its processing of mixed material streams. When shredding a car for recycling, the steel is removed first. The remaining, non-ferrous metal stream is 80% aluminum combined with copper, brass, zinc, or stainless steel. Improved separation leads to more homogenous and better-quality aluminum, Greg Palen says.
“We put in technology that allows us to do X-ray sortation — the first of its kind in North America,” Luke Palen says. “Since then, we’ve invested in other sorting technologies, improving our ability to handle a broader range of input material and ensure a high-quality finished product.”
At the same time, Spectro branched out into serving new markets, such as turf and snow maintenance, marine, and power sports. Typically, 70% of casting done in the United States goes into the automotive industry; Spectro brought its share down to 50-55% automotive to diversify its playing field and provide more consistency, Borner says.
Spectro rode out the outsourcing trend by investing in new technology and process improvements, including securing certifications in ISO 14001 for environmental management and 45001 for occupational health and safety. Staying true to its values also has been key, Borner says, plus adding novel capabilities like trading and supplying other alloys to customers to serve as a one-stop shop. “Spectro has developed a very good reputation for service and reliability,” he adds. “We’re a steady supplier that has been leading the industry in a lot of environmental aspects and international standards.”
Expansion time
During the pandemic, demand for Spectro’s recycled aluminum grew as OEMs struggled to get the raw materials they needed from overseas, coupled with soaring pricing. Customers started seeking shorter and more stable supply chains for their aluminum sheet and billet needs. That further supported the argument that Spectro should broaden its capabilities to include these new product lines, Luke Palen says.
Plans to expand Spectro’s plant got serious. Growing from 15 to 42 acres and adding new production facilities will enable Spectro to better serve existing customers and onboard new ones. The new plant will be the first of its kind in Minnesota, and it will help the company meet growing demand for green building materials and sustainable products from a local, stable supplier, Luke Palen says.
When the expansion is complete, Spectro will be able to turn beverage cans and post-consumer scrap into aluminum ingots used to make sheet aluminum. The ingots get transformed into sheet metal for automotive exteriors, beverage cans, and everything in between. Weighing up to 60,000 pounds each at 6 feet wide and 20 feet long, the ingots typically are shipped by rail or truck to rolling mills. There, high pressure machinery processes the recycled aluminum into thinner sheets.
Billet — essentially a solid log of aluminum ranging from 5 to 30 inches in diameter up to 25 feet long — is used for making aluminum extrusions. Regional extrusion customers push billet through a die of the desired shape before cutting it to length for a new product. Picture stadium bleachers, hand railings, doors and window trim, or structural frames — all commonly made from extruded aluminum. Spectro’s new plant will have the melting and casting equipment to make the necessary billet.
Adding these abilities also will help Spectro better serve the automotive market. Aluminum has been growing in importance there in the past decade as manufacturers utilize it to meet stronger fuel economy standards, Luke Palen says. Having a lighter, aluminum body compared to a steel body helps carmakers accomplish the objectives. “The Ford F-150 truck has an all-aluminum body, and other vehicles are already there with their structural components, frames, and more castings going into cars now,” he says. “The demand for aluminum content in vehicles is going up dramatically and demand for recyclable material is going up, too.”
Roadmap to success
Spectro feels confident taking on a large expansion based on its long track record of success. Establishing and maintaining a foundation of core beliefs has been an essential component of its long-standing vitality, Greg Palen says. Putting safety and people first, being customer-driven, and committing to sustainability, quality, and continuous improvement have served as guide stars during the Palens’ ownership.
“We respect people and care about people and do business with integrity,” Greg Palen says. “I think it’s allowed us to have a really good team and good people working with us. We have a lot of people who are fathers and sons or cousins, and we like that.”
Spectro’s history of providing attentive, reliable service and bringing billet manufacturing much closer to home will offer a consistent roster of business. Other midwestern companies recycle aluminum into billet, but none are in Minnesota. Plus, local manufacturers that require extruded aluminum are happy to have an additional supplier.
“This region is asking for another producer — mostly due to logistics and proximity issues,” Borner says. “Hauling scrap through three states to get it converted back to billet adds a lot of logistics costs. Being in Minnesota, we will be able to supply companies in Minnesota, Wisconsin, Iowa, and possibly others better.”
Marty Olson, an Enterprise Minnesota business development consultant who works with Spectro, observes a well-run company that attracts and retains a strong workforce of talented employees. Olson is impressed every time he visits. “They are located not too far away from a landfill, and there is a tremendous amount of volume that doesn’t go into that landfill and is repurposed,” he says. “They are a very significant recycler — the sheer volume of material they are recycling is exceptional.”
Spectro’s plan to add jobs certainly brings economic benefits. But existing employees will be gaining from the expansion, too, says Steve Haarstad, a business growth consultant at Enterprise Minnesota and leader of Enterprise Minnesota’s Monticello peer council where Luke Palen is a member. As Spectro prepares for its new facility, leadership development and job training will be top of mind. The company already has significant skilled labor, and it will augment its existing internal training and development to help current employees move into fresh roles in the new lines of business, Luke Palen says.
Other focus areas will help Spectro identify and develop current employees for leadership roles.
“We pride ourselves on training and promoting from within,” Palen adds. “Through the expansion, there will be a lot of opportunity for existing employees to expand their careers and grow into something new.”
Enterprise Minnesota President and CEO Bob Kill has seen Spectro’s broad impact when visiting other Minnesota manufacturers, like spotting shiny pallets of Spectro-labeled casting ingots waiting to be made into new components and products. It’s something he will see more of when the company’s new facility is up and running.
“Aluminum recycling used to be a manually intensive, filthy job. Over the years, the Palen family has invested in making recycling environmentally friendly. They have really led the way in recycling aluminum — the most recycled product there is, and it can be recycled many times over,” Kill says. “It’s a great story about how this family bought Spectro and grew it and continued to add technology and automation and jobs at the same time.”
Return to the Spring 2024 issue of Enterprise Minnesota® magazine.